Industrialisation
Industrialisation made Bengal famous during the ancient period. From then it was renowned as a leading international trading hub also for its world famous crafts. During the 5th century, the largest port city of Tamrolipti had trade link with South India, Ceylon (Srilanka), Malay (Malaysia), Burma (Myanmar) and countries around the Gulf of Persia and the Far East. Major industries that developed in this century in Bengal were textile, sugar, salt ivory and metal products. Arabian traders played the key role in establishing trade relations between Chittagong and the overseas destinations. Historical evidences suggest that the process of industrialisation began in Bengal far ahead of the birth of Christ. The maslins of Dhaka became popular among the royal families of the world from about 325 BC. Bengal had a worldwide reputation for its ship-building industry at that time. Its export trade before 500 AD was significant in terms of both quality and quantity. The main export items were textile and fabrics, sugar, salt and ornaments. Many handicraft-making units were established throughout Bengal by 600 AD and this sector became very rich. The trend continued slowly up to the 17th century because the artignas were engaged in making only a few products for centuries together.
The Mughal period Industrial production in Bengal experienced a marked expansion during this era as the volume of export increased gradually with the participation of foreigners, especially the European companies. The increase of production and marketing helped a lot to popularise the use of trade documents in banking and insurance sectors. During the Mughal rule in Bengal, various traditional artisan families belonging to leading professional caste of spinning wheel operator weaver, carpenter and potter, contributed a lot for the development of local industries. From the 17th century high quality textile product became one of the profitable export items. With the expansion of the market the production of sugar also increased. A remarkable progress was made in production of salt from saline water during the 17th century. Within that period, other items produced in large-scale in Bengal were agriculture implements, metal lead wares and weapons, coppers moulds ivory sculptures, woodcrafts stitching and embroidery and ornaments.
British period Prior to establishment of British rule in India, the textile sector of Bengal was completely cottage-based and the moneylenders played an important role in financing fabrics production and marketing. Weavers were given loan as earnest money by the East India Company through agencis. With the passage of time the earnest money lending system, became an adverse and repressive for the weavers as the rate of interest was high and a very low price of their products was paid in advance. These steps ultimately compelled them to give up their ancestor's profession. In 1776, the number of weavers in Dhaka district was 146751 and many more people were engaged in spinning operation in other districts. Most of the textile industries located at Maldah, Haripal and Sripur of Rajshahi, Balikushi and Kagmari of Mymensingh. Burdwan, Khirpoy and Radhanagar of Midnapore and Shantipur and Baron of Nadia district suffered decline throughout the ensuing period. Because, the British government imposed tax and non-tax bargiers on fabrics imported in England from Bengal. On the other hand, the flourishing textile industry of Britain after the industrial revolution reduced the demand for imported fabrics there.
Bengal was the centre of silk products in the British India and this industry drew much attention of the masters from the very beginning of their rule. The East India Company set up silk industries and took up initiative for cocoon cultivation in Bengal. The Company developed a mechanism for export silk from Bengal to other countries. Murshidabad was the lead cocoon growing and silk production area. A part of Murshidabad is how under Rajshahi district. The expanding silk Industry of Bengal had to suffer a setback in mid-19th century when it failed to face the competition with the cheap silk yarns imported from china and Japan and the low-priced alternate fabrics manufactured in England.
East India Company developed a dockyard in Kolkata for facilitating ship building, repairing of merchant ships and warships. Both the British and the local companies utilized the expertise of dockworkers of Bengal experience in big vessel building and trains in ship building and repairing large-scale enterprises developed in British period were jute, sugar and salt industries. The East India Company government earned a lot of money from the taxes imposed on salt trading, which ultimately created an impact, both one positive and negative, on the contemporary socio-economic condition of Bengal. The positive impact was the enhancement of salt production under the government's sponsorship and the negative side was the price of salt increased due to imposition of higher amount of tax had turned the item dear to ordinary and poor consumers. In the mid-19th country the British government fixed the import duty on foreign salt in such a rate that its price remained same as locally produced salt. That policy ultimately resulted in the process of closure of salt plants in Bengal as the quality of imported salt was betters.
In the 18th century, the leading sugar producing area in British India was Benaras. Bengal occupied the top position in the later part of the century. The price-hike of sugar in England and the fall of sugar-producing black community in Haiti and St. Domingo created a high demand of sugar worldwide including Britain. Taking this opportunity the colonial rulers began export of Bengal sugar to England and other parts of the globe. A large number of modern steam-driven sugar mills were set up by 1830 in many places to meet up the growing demand for sugar in the international market. But decline started from 1846 as Bengal sugar could not sustain in the England market due to uneven competition there. The British government increased import duty on Bengal sugar at a very high rate and deliberately changed the duty rule to that end. Moreover the colonial government in India took some measures to curb the export flow of Bengal sugar to Britain from India, which were nothing but non-tariff barriers. Moreover the price of sugar in the international market started declining due to adoption of new technology having higher production capacity in the sugar mills of Java, Mauritous and Formosa (Taiwan). As a result, the export oriented sugar industry of Bengal ultimately suffered a total collapse, as its production cost was higher thanes international market. However, the demand of sugar is the Indian domestic market was fulfilled by the products of Bengal including local variety of cheaper and nutritious mollases, prepared by juice extracted from date and palm trees. And finally, the sugar industry of Bengal could survive from the threat of extinction despite of the various developments in the international market.'
During the British rule, the industries in Bengal specially its cottage industry had earned a prominent feature of compressed specialisation due to various limitations. Mean while jute and coal industry developed. In India, specialisation of caste-based craftsmen and artisans were enriched through practice of several centuries and the standard they achieved was very rich. The British as well as local traders contributed a lot for the development of cottage industries. But in many cases, local craftsmanship was discouraged, even the artisans were physically tortured and compelled to give up their traditional occupation for accommodating the imported goods.
The Pakistan era After the portion of India, 1947, East Pakistan inherited a small share of industries owned by undivided Bengal. Out of 118 jute mills, 18 steel mills and 16 paper mills of Bengal, not a single concern was located in the territory of East Pakistan. There were only 90 spinning mills out of Bengali 389 mills, 10 sugar mills out of total 166 and 3 cement factories out of 19 similar concerns. The cement factory located at Chatak in Sylhet district had to depend on Assam of India for the supply of limestone. All the spinning mills of East Pakistan had to depend on India for raw materials. According to the Census Report of 1951, there were 63, 234 non-agricultural workers, 115, 480 skilled industrial workers, 184, 535 workers engaged in coal and stone mining and 121, 522 professional workers in East Pakistan. Out of 602, 875 Workers, 4.67% of total work force, were employed in the production sector and these comprised of mainly food, drink and tobacco processing plants. Of which, 430, 148 workers were directly involved with production process and the rest played the supportive role. There were 360,603 units of cottage industries in East Pakistan employing 949,074 artisans. Only 200 industrial units could utilise power for their production.
In the Industrial Development Policy of the government of Pakistan, production of arms and ammunition, hydro-electric power, railway wagon, telephone, telegraph and wireless were kept reserved for public sectors and the private entrepreneurship was encouraged to invest in all other sectors. Although only 24 categories of industry including jute, textile, silk and rayon were under the control of the central planning unit. The government created two specialised organisation, the Pakistan Industrial Development corporations (PIDC) and the Pakistan Industrial Finance corporation (PIFC) to promote the industrialization efforts. PIDC had played an important role in establishing industrial units in various sectors including jute, paper board, cement, fertilizer, sugar, chemical products, textile, pharmaceutical, light engineering and shipbuilding. However, the central government adopted a discriminatory policy favoring West Pakistan for its industrial development by transforming wealth and capital investment from East Pakistan. Moreover, the government invested most of the external resources in West Pakistan for its industrial development. In East Pakistan, the absence of congenial atmosphere for industrialisation was acute and as such there was no scope for capital development locally. Those who came forward to invest in East Pakistan were mostly non-Bengali entrepreneurs. The central government used to fix the prices of industrial products in such a way that the consumers of East Pakistan had to buy local products in a higher price than the products of West Pakistan. In spite of all these deliberate and discriminatory steps taken by the government of Pakistan, East Pakistan achieved a little progress in industriatlisation from 1950 to 1970. In 1970, there were 408 ford producing units, six drink manufacturing plants, 26 tobacco processing industries, 792 textile factories, 204 shoe-making units, 14 wood and cork production factories. 70 furniture making plants, 33 paper products manufacturing units, 14 printing and publication houses, 572 chemical factories. 3 petroleum and Coal-based products manufacturing units, 3 rubber factories, 53 menarel substance based factories, 35 elementary metal-based plants, 257 metallurgical units, 34 electrical goods manufacturing plants, 88 non-electrical equipment production factories, 65 communication device making units and 166 miscellaneous products manufacturing units in the then East Pakistan. However, according to the official source, 206,058 workforces were employed in 1,580 production units of East Pakistan in 1970. The net value of the products produced in that year was Rs. 3,636 billion, of which the amount of value addition was Rs. 1,708 billion. The share of industrial sector in GDP, which was only 3.9 percent in 1950 raised to 8.9 percent in 1970.
The Bangladesh era The industrial sector suffered a serious damage during the war of liberation in 1971. The reconstruction and rehabilitation cost of the damaged industrial units was estimated at Taka 291 million, of which Tk. 223 million was estimated for the public sector industries. The journey of the nationalised industrial sector began in 1972 with 72 jute mills (production capacity 79200 m ton), 44 textile mills (13.4 million pound production capacity), 15 sugar mills (169,000 m ton), one still mill (350,000 m ton), a diesel engine unit (3,000) and a shipbuilding industry. However all these industries turned into loosing concerns very soon due to mainly mismanagement and secret removal of wealth and capital. The government had to review the policy of its control over the nationalised enterprises to face the consequence. The government revised the policy and increased the investment limit of private entrepreneurs keeping its control over the industry sector. That measure did not yield any positive result. Many changes and adjustment were brought in the state policy to get a significant progress and finally the government adapted a new industrial policy in 1982 to achieve that target. Under the new policy 1,076 state-owned enterprises were transferred to private owners. The privatisation process had to suffer again because of the dearth of experience and management skill of the newly emerged rich people, who owned those mills and factories. Instead of keeping the pace of industrial development many of them started caring cash money by selling the valuable property, which they bought in a much cheaper rate. This tread mode the industry sector sick causing damage to food and allied industries (50%), (70%) textile industries, jute industries (100%) paper and paper board units (60%), rubber and leather products (90%), chemical and pharmaceutical industries (60%), glass and ceramic products (65%) and engineering products (80%).
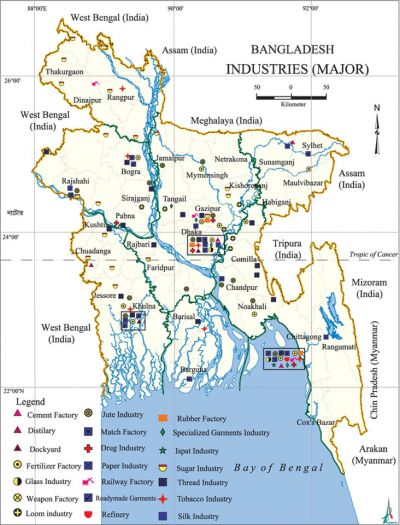
Most of the industrial units in Bangladesh belong to the small and cottage industries category. There were 932,200 units of this category in 1984, of which and handloom plants, 20.7% were 15.4% cane and bamboo crafts, 8.1% furniture workshops, 6.1% products of jute and cotton yarn, pottery- 3.4%, oilseed causing units- 0.3%, black smiths workshop- 3.2%, copper foundry-0.8% and the rest were other type of factories. Weavers live in almost everywhere of Bangladesh with extra concentration in Baburhat, Narshingdi, Homna, Bancharampur, Bajitpur, Tangail, Shahjadpur and Jessore areas. Silk industry was flourished in Rajshahi and Bhalahat. In 1980s, the following places became prominent for making handicrafts with blending of the local artisanship: Chapai Nawbganj and Islampur for Copper foundry, Sylhet for cane products and mat, comilla for pottery and bamboo crafts, Barisal for coir products and Rangpur for woven carpet.
In 1984, there were Six thousand looms and 1,025,000 spindles 58 textile mills in Bangladesh. It could produce 106.2 million pound of yarn and 63 million metres of cloth per year. The Textile industry, being a major component of nationalised sector, had to suffer a serious loss like other industries. In 1984, the amount of loss raised to Taka 353.4 million because of weak management, adverse situation for developing skill and capacity of the workers and inadequate supply of raw material and power. There were 70 juts mills with 23,700 spindles in Bangladesh in the same year. Then the mills had 168,000 workers and 27,000 other staffs.
The mills used 545,000 m ton of raw jute in that year. But this year's total production was much lower than the production of 561,000 m ton in 1969 by 55 jute mills of 21,508 spindles. Dhaka, Chittagong and Khulna were the main centres of jute industries. By now, comparatively cheaper and more durable plastic products have replaced jute goods. Moreover, the jute industry of the country in being reduced in the context of changed global condition and the competition against India.
The development of new industries like sulfuric acid, chemicals, paper, costic soda, glass, fartiliser, ceramic utensils, cement, still and engineering was slow before 1985. There were only two production plants of sulphuric acid, used as an element in soap, paper, iron foundry and still mills, in the country in 1985. Those had a production capacity of 5,995 m ton per year, though in 1970 the production of these elements was 6'466 m ton. The production of costic soda in 1985 was 6,787 m ton and almost the whole back was used in paper mills. Bangladesh is a highly potential country to be a leading glass manufacturing nation as it has abundant reserve of sand, salt and limestone. Meanwhile a number of glass factories, set up in and around Dhaka and chittagong, have started production. An automatic glass factory, established at Kalurghat in Chittagong had produced 12.9 million square feet of glass sheets in 1985.
Natural gas is used as the main raw material for producing fertilizer. In 1985, the country's total fertilizer production was 808,660 m ton, of which Urea was 741, 463 m ton, Amonium Sulphute 9,634 m ton and Triple Super phosphate (TSP) was 57,563 m ton. Fenchuganj, Ghorasal and Ashuganj are the locations of the countries three big fertilizer plants. The country's cement factories including two gigantic plants located at chatak and Chittagong had produced 292,000 m ton of cement in 1985. Total production of paper in 1985 was 75,000 m ton and two big paper mills were set up one each is Chandraghona, of Chittagong and Pakshi of Pabna. A newsprint mill and a hardboard mill were established in Khulna and these plants had produced 55,000 m ton of newsprint and 1,621 Square metres hardboard respectively in 1985. There were some particle board and pertex producing mills in Bangladesh in 1985. The country was also self-reliant in match production. Dhaka, Khulna, Khepupara, Chittagong, Sylhet, Bogra and Rajshahi were main centres of match box production. In 1985, 1.3 million gross (12 dozen=1 gross) of match boxes were produced. In the same year, 87,000 m ton of sugar was produced by eight sugar mills of Bangladesh. The Darshana sugar mills in Kushtia also produced Alcohol, Methylated spirit and rectified spirit. The government owns most of the iron and steel mills of Bangladesh. There are concentrated in Dhaka and Chittagong as enterprises under the Steel and Engineering Corporation.
New industrial ventures set up in the 1980s in Bangladesh have been playing a significant role in the countries economy. These include, shipbuilding industry, motor vehicle assembling plant, oil refinery, insulator and medical equipment manufacturing factories, telephone and telecom accessories making units, televisions assembling factories, cigarette factory and vegetable oil industries. Readymade garment sector achieved a remarkable progress in the country during the period. The government followed a strategy of mixed policy comprising of the open market economy and the national development plan. As a result, the industrial growth raised to a significant stage in the 1990s and the contribution of industries sector to the GDP increased to eleven percent. Total investment in this sector, was raised to Taka 57.8 billion in 1997 from that of Taka 22.5 billion in 1991. Of the total industrial investment of 1991, the government share was 37.03%, which reduced to 8.63% in 1997. According to the last industrial survey, conducted in 1991, data of industrial production are as follows:
The government has been continuing its privatisation programme to handover the nationalised industries under private ownership. In 2000, one cement factory having the annual production capacity of 0.15 million m ton, one paper mill of 30,000 m ton capacity, one newsprint mill (52,000 m ton), Six cigarette factories (630 million sticks), eight oil mills (938,818 m ton), two food processing plants (950,400 m ton), two fish processing plants (6.9 million m ton), two cold storages (5.9 million pound), one drinks bottling plant (4.3 million bottles), three chemical product units (65,100 m ton), one glass factory (7.5 million square feet) and twelve pharmaceutical industries belong to the government, were identified as sick industries and brought under the sick industry rehabilitation programme. In the 5th Five-year plan (1997-2002), Taka 8.95 billion was allocated in industry sector, of which 1.39 million taka was earmarked for private enterprise. Total number of staff and workers employed in industry sector in 2000 was 0.6 million, of them 0.5 million were appointed in private sector industries.
Table Industrial production in 1991.
New industries set up division-wise | Price of products and by-products (million Taka) | ||
Total | 26,446 | 2,13,073 | |
Dhaka | 11,790 | Final Products | 2,10,301 |
Chittagong | 3,791 | By-Products | 2,628 |
Rajshahi | 7,765 | --- | 144 |
Khulna | 3,100 | --- | --- |
Net Wealth (in Million Taka) | 10,2415 | Paid Tax (in Million Taka) | 11,298 |
Number of Staffs | --- | Total Production (in Million Taka) | 2,22,868 |
Total | 11,56,204 | --- | --- |
Male | 9,79,328 | Total Value added (in Million Taka) | 73,249 |
Female | 1,76,876 | ||
Man Power employed | --- | Value addition on expenditure of production elements (in million Taka) | 51,090 |
Total | 13,27,287 | ||
Male | 11,28,905 | ||
Female | 1,98,382 |
In the 1999s, the government's initiatives for industrialisation included investment for balancing, modernisation and reconstruction, creation of new industrial parks and export processing zones, promotion of private investment and encouragement of foreign direct investment (FDI). Various changes were made in the industrial policy in line with the trend of international market and the integrated programme undertaken following the recommendation of agencies concerned and development partners to liberalise the trade and investment. The government has been formulating a new industrial policy for every 4-6 years period from 1982 incorporating provisions for providing increased incentives to local and foreign investors. Mains features of these policies are to encourage industrialisation in remote rural areas, to motivate entrepreneurs for using local raw materials and technology and to extend support for finding out ways and means to transfer technology. [M Habibullah]